The technical meaning of CMMS software or computerized maintenance management system, includes performance review, service, repair or replacement of necessary devices/parts, equipment, machinery, building infrastructure, and support facilities in industrial, commercial, government, and residential facilities.
What is CMMS software?
CMMS software or Computerized Maintenance Management System, is a software package that maintains a computerized database of information related to an organization’s maintenance operations.
This information is used to help maintenance and repair staff to perform their jobs more effectively (e.g. determining which machines need maintenance and which warehouses have spare parts). Also to help management make informed decisions (e.g. calculating machine breakdown repair cost versus preventive maintenance for each machine that leads to a better allocation of resources).
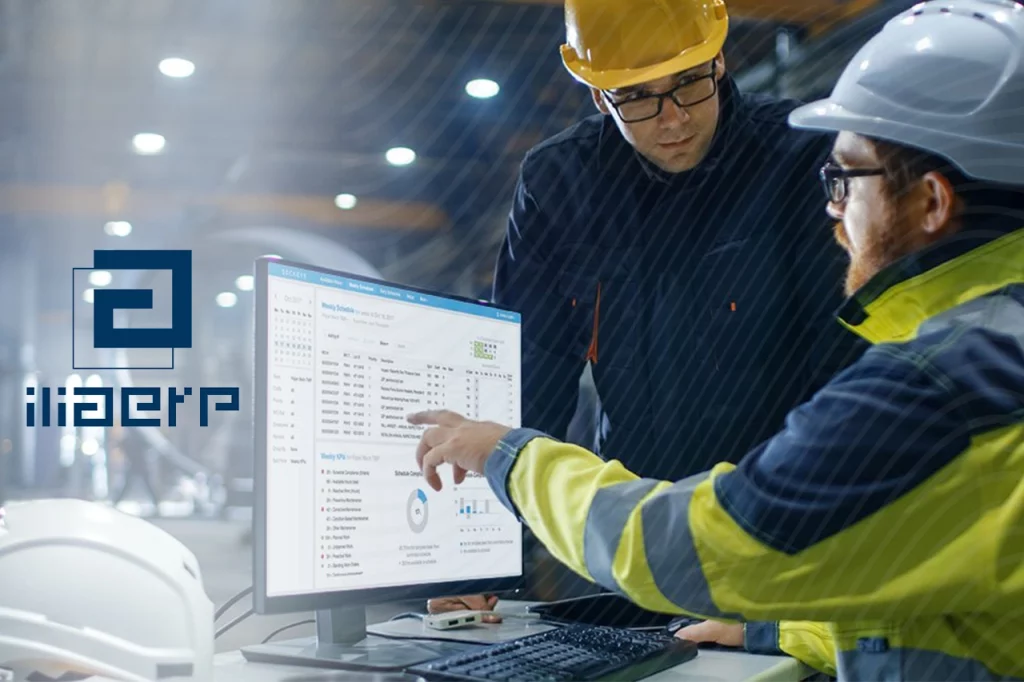
Need to say that CMMS software data may also be used to verify compliance with maintenance and repair laws and standards. To properly control the maintenance of the facility, information is used to analyze what is happening. Also, if this is done manually, it requires a lot of effort and time.
CMMS also provides the possibility of registering records, tracking completed and assigned tasks in a timely and cost-effective manner. Recognizing this, organizations have started using CMMS to better control and organize maintenance management.
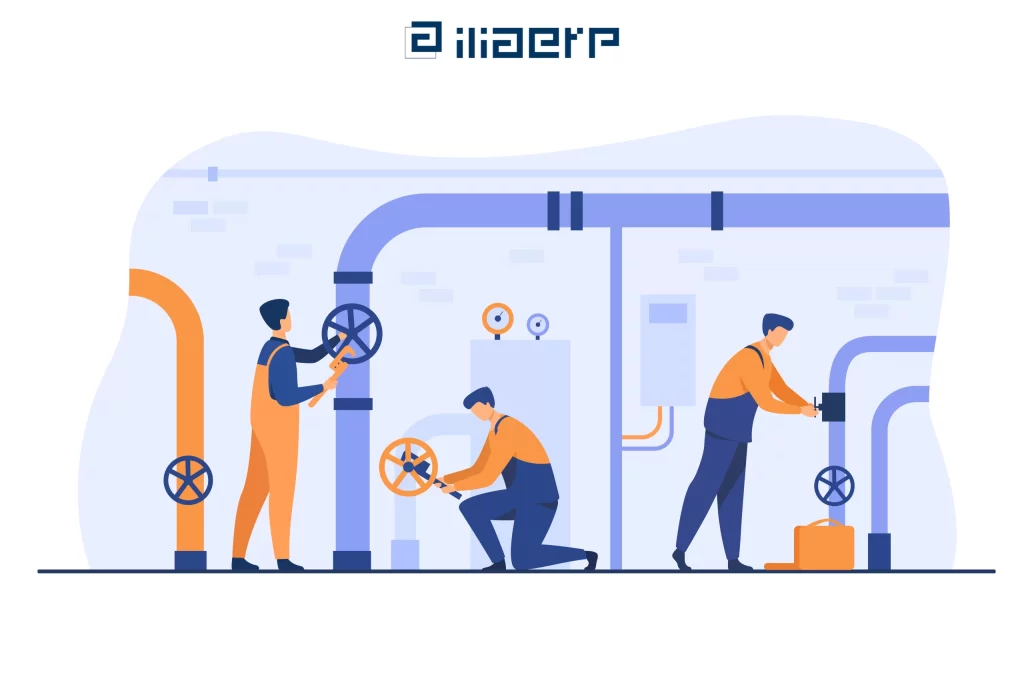
Multimodal maintenance:
CMMS software also offers multifaceted maintenance features that cover all industries. Facilities, transport or logistics fleets, hospitals, sports industries and many others that have any type of equipment/asset under repair and in need of repair are included in this category.
As technology advances and competition increases, more companies today are using CMMS as opposed to using manual methods to track and organize information.
Common components of CMMS software:
- Equipment data management
- Preventive maintenance and repairs
- Predictable repairs
- Work order system
- Planning
- Seller management
- Inventory control
- Purchase
- Budgeting
- Asset tracking
In fact CMMS software may be used by any organization that needs to maintain and repair equipment and assets. Some CMMS products focus on specific sectors of the industry (for example, vehicle fleet maintenance or health facilities), but other products are usually aimed at a more comprehensive use.
Plus CMMS packages can provide status reporting (details or summaries of maintenance activities). The more extensive this software is, the more extensive analysis facilities it provides to the organization.
CMMS system based on cloud processing
Many CMMS software can be cloud-based, meaning hosted on a server outside of your organization. In this case, there is no need to provide the necessary hardware to implement a maintenance and repair system inside the organization.
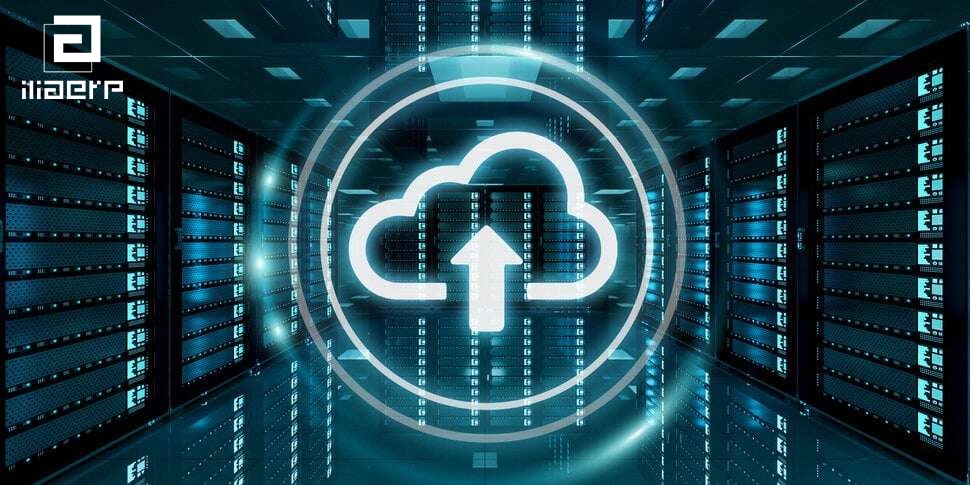
History of CMMS
Before CMMS, achieving centralized and dynamic visibility and automated management of maintenance processes was not practical because maintenance information was scattered in paper files or Excel files.
The first versions of CMMS were developed in the 1960s and were typically used by large companies. Technicians used punch cards and IBM mainframes to access computer records and track maintenance tasks. In the 1970s, punch cards gave way to checklists entered into CMMS systems by technicians at the end of their shifts.
In the 1980s and 1990s, CMMS gained popularity in small and medium-sized businesses as computers became smaller, more affordable, more distributed, and more connected. Also in the 1990s, CMMS began to share information on local area networks.
The 2000s saw the advent of intranets and web connectivity, which extended CMMS capabilities to a wide range of mobile devices, field applications, and operational sites.
Latest generation of CMMS is also cloud-based, which has better performance, faster implementation, easier maintenance and repairs, and more information security.
What are the benefits of CMMS?
Ability to view assets:
Centralized information in the CMMS database enables managers and maintenance teams to immediately gain complete information on their current status when purchasing assets, performing maintenance, failure rates, parts used, performance ratings and more.
Workflow view:
The management dashboard provided by the system can be configured with technician and other roles to assess status and progress in real-time. Using this system, maintenance teams can quickly discover where the asset is located in the organization, what it needs, who needs to work on it, and when.
Automation:
Automating manual tasks such as ordering parts, renewing MRO inventory, managing shifts, gathering information for audits, and other administrative tasks saves time, reduces errors, improves productivity, and allows teams to focus on maintenance (rather than administrative) tasks.
Simple processes:
With this software, work processes can be observed and tracked by all parties involved, details can be shared on portable equipment such as mobile phones to coordinate work in this field with operational centers. Distribution and use of materials and resources can be prioritized and optimized.
Field workforce management:
Managing internal and external workforce can be complex and costly. CMMS capabilities can unify internal teams and external partnerships cost-effectively. The latest CMMS solutions have made advancements in connectivity, mobility and blockchain methods to transform operations in this field.
Preventive maintenance and repairs:
CMMS data enables the maintenance department to move from a reactive to a proactive approach, on which an advanced asset maintenance strategy can be developed. Data from day-to-day activities as well as sensors, meters and other IoT tools can provide insight into processes and assets, inform preventive actions and generate alerts before assets fail or underperform.
Compatibility and knowledge transfer:
Documents, repair manuals and maintenance procedures can be stored in the CMMS and linked to the relevant assets. Acquiring and maintaining this knowledge creates consistent procedures and practices. It also allows knowledge to be transferred to new technicians instead of being lost with personnel who leave.
Compliance Management:
Basically compliance audits can be disruptive for maintenance operations and high-use jobs in general. CMMS data makes this massively easy by generating response and reporting tailored to audit demands.
Environment, safety and health:
In fact Compliance management CMMS provide central reporting for safety, health and environmental concerns. The purpose of this is to reduce risk and maintain a safe operating environment. A CMMS can perform investigations to analyze recurring incidents or defects, incident tracking and corrective action capabilities, and process change management.

We at Ilia ERP Corporation have created the ability to support this software with maximum reliability by the technical team within the company by providing a valid license in the name of your organization from Focus Company by institutionalizing the technical knowledge of this software in our company.
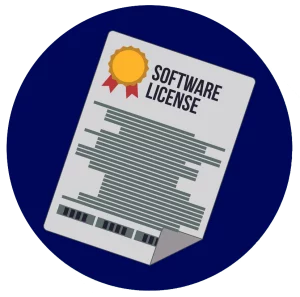
Focus CMMS or maintenance management software
FOCUS Softnet’s ERP solutions have a comprehensive CMMS software (maintenance and repairs management module) that helps your organization to increase operational efficiency in your industry. This solution is the most complete by considering various aspects of the process in the field of maintenance and repairs. The comprehensive process provides a system of maintenance and repairs.
Also, due to its facilities and modern infrastructure, this system brings the convenience of users in using the minimum required resources.
Focus ERP’s received awards from prestigious organizations in 2021
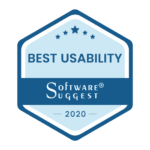
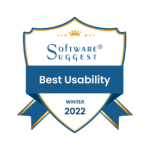
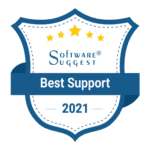
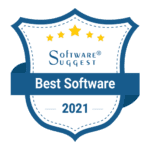
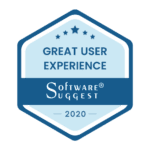
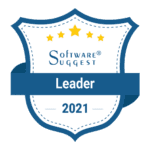
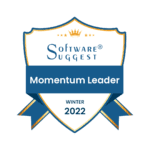
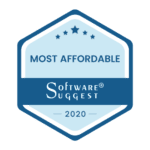
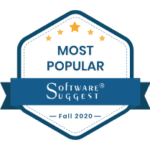
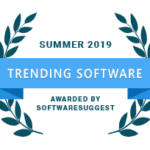
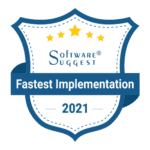
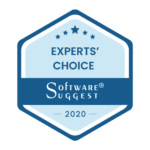
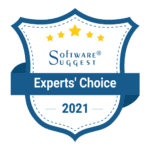
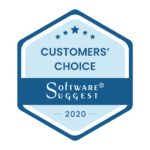
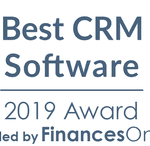
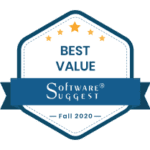
Key features of FOCUS CMMS software
- Online schedule management tables
- Check list
- Periodic service management of the device
- Setting internal processes with software for control
Focus CMMS module includes scheduling, sending and generating service orders, tracking staff expertise and service invoices. Also, by using this software, you can easily check whether a service is provided based on the guarantee or not.
The Focus maintenance management module enables users to easily manage day-to-day operations along with monitoring equipment that need maintenance, ensure customer quality service through integrated verification services, and obtain comprehensive management analysis report.
Register your free software consultation request now.
Our experts will respond to your request in the shortest possible time.
Why do industries need CMMS software (repair and maintenance software)?
- Service checklist
Ensuring that no part of service functionality is bypassed through existing sensitive checklists.
- Equipment periodic service
Schedule and initiate maintenance and repairs for each piece of equipment detailing which pieces of equipment require service and when.
- SLA, service level and maintenance
Ensuring service levels and reactive maintenance as well as initiating planned preventive maintenance when necessary.
- Customer relation management
Improving relationships with customers, providing strong and reliable support
- Smart reports
Detailed and personalized reports in the form of complete business summaries
- Human resource planning and management
Simplify workforce management with simple automated attendance tracking tools and timesheet management for all technicians
- Inventory management
Inventory control of spare parts and parts
- Accounting and billing
Integrated accounting software